As soil embankments are constructed, the fill is spread in layers and compacted in order to increase strength and reduce compressibility of the soil. The loose lift thickness is usually 8 inches to 12 inches. These photos show four different types of rollers suitable for compacting cohesive (clayey) soils and cohesionless soils (sands and gravels).
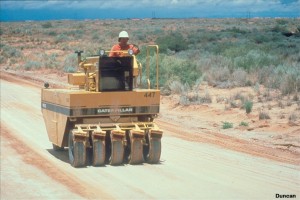
Here a pneumatic rubber-tired roller is compacting clay soil. Clays are more difficult to compact than sands and gravels, because they must be brought to the right range of water content before they can be compacted to high densities. Static pressure, as exerted by the wheels of this rubber-tired roller, compacts clays well. (Photo by Caterpillar).
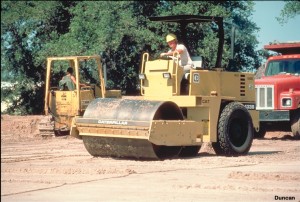
This photo shows a vibratory steel-wheeled roller compacting sand. Vibration is more effective for compacting sands and gravels than static pressure. Water conditioning is not as important for compacting sands and gravels as it is for compacting clays. The total force applied by a vibratory roller is equal to the weight of the roller plus the dynamic vibratory force. (Photo by Caterpillar).
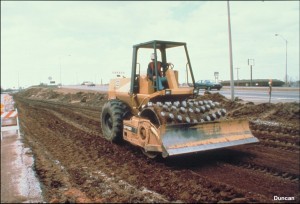
Here a vibratory padded drum roller (similar to a sheepsfoot roller) is compacting clay. The protrusions (pads) on the drum press into the soil when it is loose, and compact the layer from the bottom up. After a few passes, when the fill has been densified to some degree, the roller “walks out,” and the entire weight is supported on the pads resting on top of the fill, which results in higher compaction pressures on the soil. (Photo by Caterpillar).